Earlier this summer our marketing team headed down to Downpatrick in County Down to spend the day at Northern Irish brand Finnebrogue to make a case study video. Here's what we got up to while we were there...
The relationships we forge with our customers are a really important part of how we work. So when Finnebrogue said we should come down and chat to them about their experiences of going through digital transformation we jumped at the chance.
Our aim was to discover how our partnership with this leading food producer had changed how they worked. We went equipped with a small crew, lots of questions and the hope that the sun would shine down on our shoot.
Preparing for the shoot
The poppies waved in the breeze, as we set up our cameras in the Finnebrogue roof garden, preparing for the interviews and making sure the sun was in the right place for our shots. Behind us the company chef collected rosemary for that afternoon’s lunch menu and down below, Finnebrogue lorries rumbled along the roads carrying sausages and bacon off to new destinations.
Once Laura Robinson and Catherine McGrath – two of our three Finnebrogue interviewees for the day – were miked up, we were ready to break the ice. Putting them at ease was an important part of the process.
We started to chat about their experiences of the Foods Connected software. Raw Material Technologist, Catherine, whose role includes the approval process for all the food business’ new suppliers, opened up about the time savings she’d experienced since working with our software solutions. In her four and a half years at the company, her career high point was the opening of the state-of-the-art vegan factory with its 200-plus unique ingredients, a process we had helped them achieve. This task was all the more impressive because it had happened in the middle of the pandemic and without increasing the workforce.
Next in the hot seat was Laura. As Head of Technical at Finnebrogue, she was particularly busy as an audit was going on in the vegan factory that day. But she was calm and collected in front of the camera, making sure we had the time we needed to talk through her process.
No "whizzkid" IT skills needed
During our chat, Laura happily admitted that she's no IT whizz, but from the very first time she met with the Foods Connected team, she knew that ours was a system she could use. And she said that if she did have questions, the Foods Connected team were always on standby and ready to help, commending our willingness to jump on calls even during the pandemic.
Finnebrogue works with some of the biggest retailers in the UK and this had been one of the big drivers to change the way they worked. As Laura talked to us about the digitisation process, she also touched on the issue of finding the right talent for the business. She admitted that by using Foods Connected her team were able to accomplish the tasks in hand without hiring anyone else - a real bonus when it's difficult to find people with the right skill set for the technical jobs needed.
With our first two interviews completed and some drone shots captured to get an overview of the Finnebrogue facility, it was time to find our third subject of the day - compliance auditor Amy Irvine. Amy had completed her placement year at Finnebrogue as a quality auditor on the factory floor and then returned last year to take up her compliance auditor role.
Trending made easy
She uses the Foods Connected software on the factory floor and loves how it saves her time with trending and audits. We were able to see her in action overseeing sausage production, getting results in real-time thanks to our software functionality.
The time flew by as we walked the floor in our regulation hairnets, boots and white coats, watching the different teams working the production lines and ensuring that everything was of the highest quality. Anything that didn't comply was immediately removed in line with Finnebrogue's strict quality procedure.
And before we knew it our day of filming was over. All that was left was to say our goodbyes and thank everyone for their time. Now all we had to do was edit the footage.
Watch a sneak peek of the final video below...
Watch the final case study video here.
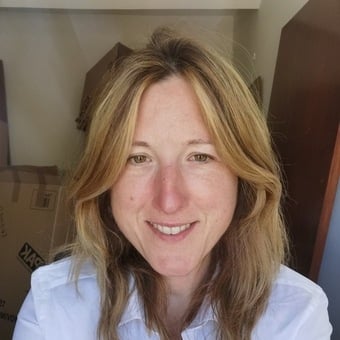
Greer McNally
Greer has over 15 years’ experience writing about trends in the food and retail sectors. She lives in a little village by the sea in Northern Ireland and loves creating content that informs how people think about the food industry. A recent career highlight was interviewing the legend that is Dr Temple Grandin.
Stay up to date
Stay up to date
Browse Posts
- September 2025
- August 2025
- July 2025
- June 2025
- May 2025
- April 2025
- March 2025
- February 2025
- January 2025
- December 2024
- November 2024
- October 2024
- September 2024
- August 2024
- July 2024
- June 2024
- May 2024
- April 2024
- March 2024
- February 2024
- January 2024
- December 2023
- November 2023
- October 2023
- September 2023
- August 2023
- July 2023
- June 2023
- May 2023
- April 2023
- March 2023
- December 2022
- November 2022
- October 2022
- September 2022
- August 2022
- July 2022
- June 2022
- May 2022
- April 2022
- March 2022
- February 2022
- January 2022
- December 2021
- November 2021
- October 2021
- August 2021
- July 2021
- June 2021