In this case study we explore how Freshpak replaced manual systems with a connected, digital solution - streamlining audits, improving traceability, and creating a more efficient way of working with Foods Connected.
About Freshpak
Freshpak is a leading supplier of chilled foods to major UK retailers and food service providers. Renowned for its high-quality standards, the business manages complex operations and strict compliance demands across manufacturing.
With increasing pressure to improve traceability, audit readiness, and supplier management, Freshpak recognised that its manual systems - paper trails, spreadsheets, and emails - were no longer fit for purpose.
Manual processes are holding back progress
Before adopting a digital solution, Freshpak’s processes were fragmented and time-consuming. Departments operated on paper-based forms and spreadsheets, making it difficult to track issues, monitor compliance actions, or maintain a clear view of operational performance.
Some key challenges included:
- Logging fabrication issues could take up to 20 minutes, delaying resolution.
- Internal audits required hours of preparation, with data scattered across systems.
- Senior management lacked visibility into outstanding actions and non-conformances.
- Teams were spending time on admin rather than proactive improvements.
These inefficiencies created pressure, particularly during audits or investigations where fast access to accurate data was essential. It was clear that Freshpak needed a connected, digital-first approach that would enable real-time insights and faster decision-making.
Flexible, connected, and built for the food industry
Rather than force their processes to fit into a rigid system, Freshpak found a platform that could adapt to their existing ways of working—and help improve them over time.
Key areas of transformation included:
- Internal Audits & Compliance Tracking – All audit activities are now managed digitally, enabling faster reporting, easier follow-up, and better traceability.
- Supplier Management – Issues with suppliers can be logged instantly and tracked to resolution. This reduces response times and strengthens risk management.
- Cross-Departmental Visibility – Teams across Technical, NPD, H&S and Production now operate within the same system, using shared dashboards and real-time updates.
- Self-Service Configuration – Freshpak’s teams can build and update their own forms, workflows and dashboards—without needing to rely on IT.
“With Foods Connected, we found a flexible system that could grow with our intent to grow our own business.”
– David Green, Technical Director, Freshpak
This ability to customise the system internally has helped Freshpak build greater ownership and accountability across teams, while also reducing reliance on third-party configuration support.
Faster processes, fewer complaints, and a more empowered team
The impact of the transformation has been felt across Freshpak’s operation:
Faster, Smarter Workflows
The time to log fabrication issues has dropped from 20 minutes to under 20 seconds—a 98% reduction. With a more streamlined workflow, teams can focus on resolving problems rather than chasing paperwork.
Stronger Audit Performance
Audit preparation is now 40% faster, with relevant data easy to retrieve, cross-reference and present. Freshpak is consistently audit-ready and have reduced their time spent with any pre-audit preparations.
Reduced Customer Complaints
In 2024, Freshpak achieved its lowest ever level of customer complaints. The improved issue tracking and real-time monitoring helped the business detect and resolve non-conformances before they escalated.
Greater Team Engagement
Empowering team leads to build and manage their own processes has increased engagement and accountability. Staff are no longer tied to admin-heavy routines and are encouraged to contribute to continuous improvement.
“There is nothing more empowering than seeing improvements you’ve instigated take shape.”
– David Green, Technical Director, Freshpak
A platform that grows with the business
Freshpak’s digital transformation isn’t a one-off project—it’s an ongoing evolution. The company continues to expand how it uses Foods Connected’s tools across new departments and processes.
The focus now is on:
- Integrating more departments into the platform for full operational visibility
- Using data insights to drive further efficiency and performance improvements
- Maintaining a culture of ownership and accountability at all levels
By choosing a flexible, food-specific platform, Freshpak has future-proofed its operations and built a foundation for growth. In a highly regulated and fast-moving industry, this level of adaptability is what sets them apart.
If you'd like to discover more about how Freshpak transformed their supplier management, you can get your own copy of the full case study here.
Want to learn how we can help transform your processes? Click below to book a free demo and chat with one of our team
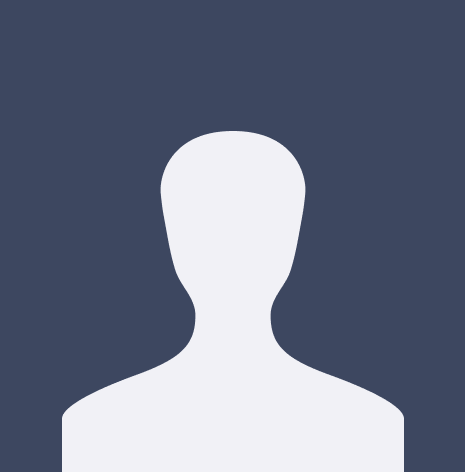
Caitlin Arthurs
Caitlin Arthurs is a Marketing Executive at Foods Connected, specialising in content creation, SEO, and digital strategy. She works closely with industry experts to produce insightful articles, case studies, and resources that help food businesses optimise their operations and stay ahead of regulatory changes. When she’s not crafting content, Caitlin enjoys graphic design, travelling, and spending time with her golden retriever, Spencer.
Stay up to date
Stay up to date
Browse Posts
- September 2025
- August 2025
- July 2025
- June 2025
- May 2025
- April 2025
- March 2025
- February 2025
- January 2025
- December 2024
- November 2024
- October 2024
- September 2024
- August 2024
- July 2024
- June 2024
- May 2024
- April 2024
- March 2024
- February 2024
- January 2024
- December 2023
- November 2023
- October 2023
- September 2023
- August 2023
- July 2023
- June 2023
- May 2023
- April 2023
- March 2023
- December 2022
- November 2022
- October 2022
- September 2022
- August 2022
- July 2022
- June 2022
- May 2022
- April 2022
- March 2022
- February 2022
- January 2022
- December 2021
- November 2021
- October 2021
- August 2021
- July 2021
- June 2021