In 2022, reports began that a shortage of farm labour was having implications across the UK. We will trace how this has impacted the food industry in 2023.
Labout shortages have been an issue for the farming and food industries for some time now. But they garnered significant attention at the end of 2021 and have continued to have ramifications throughout the following year. Broadly summarised, a scarcity of labour has disrupted supply chains, resulting in high costs and excessive waste.
In this article, we will be surveying the impact of labour shortages in 2023 and how manufacturers, suppliers and retailers can begin to recover.
What type of labour shortages have the food and farming sector experienced?
Due to a range of factors, including the COVID-19 pandemic, Brexit and stricter immigration laws, farms across the UK have experienced a shortfall of seasonal workers. The food and farming sector is highly dependent on seasonal workers, especially during harvesting time.
Although the UK government had previously extended seasonal work visas at the start of 2022, this has not fully addressed the labour gap. As a result, industry profits have been impacted by a reduction in crop yields. Furthermore, a UK parliamentary inquiry at the end of 2021 found that the food industry was also suffering from a reduction in HGV drivers, as well as problems recruiting staff for food and drink processing facilities. These have caused bottlenecks in the food supply chain, delaying the provision of goods whilst also driving up transportation and delivery costs.
How much did labour shortages cost the food and farming sector in 2022?
Based on reports from industry associations, regulatory bodies and government agencies, it has been estimated that labour shortages have cost the UK over £60m in wasted food. This unfortunately does not account for costs associated with reduced productivity, delays in the supply chain, cancelled deliveries or products not being available on supermarket shelves.
Have labour shortage costs improved in 2023?
The uncertainty surrounding seasonal work visas, coupled with the after-effects of Brexit and the pandemic, means the food industry is still paying significant amounts due to labour shortages.
A 2016 report from the Agriculture and Horticulture Development Board estimated that EU workers once made up 20% of the permanent workforce in British agriculture and horticulture. However, in the years following the initial Brexit decision, this supply of labour has continued to deplete. This was reflected in a 2023 survey of the National Farmers’ Union, in which 41% of respondents reported having reduced their food production due to the shrinking workforce.
On top of all that, the demand for skilled workers across other industries continues to increase, leading to even greater difficulties in hiring and retaining skilled agricultural workers. In summary, the impact of labour shortages on the food and farming sector remains considerable in 2023.
How has the food industry dealt with farm labour shortages?
Manufacturers, retailers and service providers have been under pressure to streamline processes and reduce costs. While one approach has been to invest in automation and technology, this is not feasible for many companies who are straining under the financial burden of labour shortages. For these companies, a more viable solution has been to optimise their existing resources. This has meant evaluating their processes to help streamline operations, reduce waste and enhance efficiency without having to make costly investments.
Another mitigating tactic has been to lobby for more favourable immigration policies that can provide access to a wider pool of workers. While this strategy may not see substantial results in the short term, gradual policy change may be the solution needed to fully replenish the food and farming workforce in the years to come.
Finally, some companies have begun offering competitive incentives to attract and retain workers. While smaller providers and companies facing financial difficulties may not be able to offer higher wages or bonuses, they could consider flexible working arrangements, mentorship and career development as potential incentives for prospective employees.
How can food manufacturers, retailers and service providers recover the cost of labour shortages?
To recover costs associated with labour shortages, food manufacturers, retailers, and service providers can implement various strategies. For example, one way to mitigate the impact of labour shortages is to diversify supply chains. Consistently relying on the same supplier leaves your business vulnerable to disruption; widespread reliance can even disrupt an entire industry, as we saw during the US baby formula shortage of 2022. By establishing relationships with multiple suppliers, companies can ensure a highly robust and resilient supply chain.
As previously mentioned, a valuable long-term solution could be training and upskilling the local workforce. By providing education and training programs, businesses can equip individuals with the necessary skills and knowledge to fill labour gaps. This not only helps alleviate shortages but also contributes to the development and growth of the local community.
Addressing labour shortages industry-wide undoubtedly requires a multi-faceted approach. For those who are ready to start addressing labour issues using technology, our Food Supplier Compliance Management Software allows suppliers to audit workflows and closely manage risk throughout the entire process. Our software is modular and therefore can be scaled to work with your existing resources or address specific needs. This helps make it more accessible for businesses who are looking to avoid large upfront costs.
To learn more about how Foods Connected can work for your business, request a demo today.
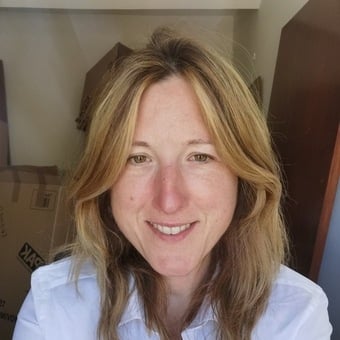
Greer McNally
Greer has over 15 years’ experience writing about trends in the food and retail sectors. She lives in a little village by the sea in Northern Ireland and loves creating content that informs how people think about the food industry. A recent career highlight was interviewing the legend that is Dr Temple Grandin.
Stay up to date
Stay up to date
Browse Posts
- August 2025
- July 2025
- June 2025
- May 2025
- April 2025
- March 2025
- February 2025
- January 2025
- December 2024
- November 2024
- October 2024
- September 2024
- August 2024
- July 2024
- June 2024
- May 2024
- April 2024
- March 2024
- February 2024
- January 2024
- December 2023
- November 2023
- October 2023
- September 2023
- August 2023
- July 2023
- June 2023
- May 2023
- April 2023
- March 2023
- December 2022
- November 2022
- October 2022
- September 2022
- August 2022
- July 2022
- June 2022
- May 2022
- April 2022
- March 2022
- February 2022
- January 2022
- December 2021
- November 2021
- October 2021
- August 2021
- July 2021
- June 2021