Planning is integral for any effective supply chain. In this guide we summarise why and explore the benefits and best practices of supply chain planning in the food industry.
The purpose of supply chain planning (SCP) is to achieve an optimal balance between supply and demand, linking businesses, suppliers and customers to meet market demand as efficiently and economically as possible.
In the food industry, careful planning is required to achieve this aforementioned balance - optimising the delivery of goods and the exchange of key information. As a future-focused activity, SCP provides a roadmap that can be followed in the day-to-day process of supply chain execution.
This article will examine the core components of an SCP system, elucidating the role of specific planning methods and technologies while also exploring the benefits and challenges of SCP with a particular focus on the food and beverage industry.
What are the main types of supply chain planning?
There are four primary supply chain models, each one entailing different planning procedures and suiting specific product categories depending on the nature of consumer demand. In the food industry, businesses may use more than one model depending on product type.
Demand for some products can be steady for most of the year, spiking during particular seasons. For instance, chocolate is always in demand, but it’s especially popular in the run-up to holidays such as Mother’s Day, Valentine's Day and Christmas. For most of the year, a continuous flow model is effective, but during these peaks, the efficient model may be more appropriate.
The continuous flow model
Some products such as staple foods are constantly used and replenished with relatively stable demand. In this scenario, continuous flow models keep supply chains moving at a balanced pace, meeting an ongoing consumer demand that is relatively uniform in nature.
The fast model
This model is applicable when demand for your products shifts quickly based on consumer trends and preferences. Although the fast model typically applies to high fashion and consumer electronics, it can also apply to food supply chains (a hallmark example of this being the transient craze for “edible glitter" in 2018).
If speed and responsiveness to varying demands are a feature of your products, the fast model may apply. For example, a new product introduction can stimulate a great deal of consumer interest. In the fast model, minimising delivery times to prevent stock shortages will be a priority.
The efficient model
The efficient SCP model occupies a space between the continuous flow model and the fast model. In essence, demand is continuous but also subject to fluctuation. In food businesses, this fluctuation is often seasonal. For example, packaged soups are more popular in winter, but there’s still some demand for them during the summertime. This model ensures sufficient inventory for both consistent product delivery and fluctuating demand.
The custom-configured model
A custom-configured model refers to products that are made to order with some level of customisation. For example, a catering company will not hold finished products as inventory and they will limit stocks of ingredients. They wait for customers to place their orders before acquiring most of the necessary inputs. Rather than prioritising speed, this model is conducive to a methodical approach to supply chain management based on customer input.
What are the main components of a supply chain planning system?
Demand planning
As a logical starting point, demand planning focuses on forecasting demand, allowing supply chains to prepare accordingly. Previously, forecasts were based primarily on historical sales and market trend data. However, this fails to compensate for data that may be inaccurate or unavailable, not to mention factors like the “bullwhip effect” which skews perceptions of demand.
For example, a retail chain may opt to attract customers by reducing prices on a specific product. If their wholesaler doesn’t know why the retailer is suddenly ordering more stock, they might assume it’s a new trend and increase stock levels. This knock-on effect travels back along the supply chain, increasing in magnitude as suppliers add an extra margin of safety to their inventory. Demand then falls sharply as customers stock up on the product. This leads to what seems to be fluctuating demand even though consumers still use the same amount of a certain product as they always did in the past.
Demand-driven supply chain planning helps food businesses prevent the two inventory issues most likely to have a negative impact on their businesses: stockouts and excess inventory. This can be achieved through data modelling based on real-time analytics, supply chain data and automated information sharing.
Supply planning
Once you have determined the expected demand, supply planning prepares your business to meet it. To do so, you must plan for production, capacity, inventory, sales and operations. Once these have given you a clearer picture of how you will meet demand, it will be time to design and optimise the supply chain with input from selected supply chain partners.
Production planning
This form of planning allows you to see what your business is required to do to meet market demand. Production planning consists of formulating production schedules, determining how resources would be allocated and identifying which workflows would be activated.
Capacity planning
In parallel with production planning, your team will analyse whether your business has the capacity to meet expected demand. Current capacity is compared to expected demand, and if there are shortfalls, capacity planning seeks to address these. For example, it may be possible to optimise production processes, invest in additional equipment, or outsource production.
Sales and operations planning (S&OP)
Sales and operations planning uses capacity forecasts to determine how your business will meet demand. It aligns sales forecasts and production plans, evaluates how financial goals are impacted, and determines how resources would be allocated.
Inventory planning
So far, the process has worked back from demand forecasting, determining what must be done and setting timeframes and methods that will allow your business to meet demand. You now have a downstream supply chain plan, but upstream supply chains will also be crucial to delivering the inputs needed to execute your plan.
Inventory planning sets out a framework that includes reorder points, safety stock, and expected inventory turnover. In short, your inventory planning specifies what you require from your suppliers and how much inventory you will hold. This information is used to communicate needs and collaborate with potential suppliers.
Supply chain network design and optimisation
Supply chain network design determines the upstream and downstream movement of inputs and products to and from your business. In the food industry, supply chain networks tend to be complex. Optimisation factors include price, quality, regulatory compliance, logistics, efficiency, sustainability, and risk management. End-to-end SCP ensures that upstream and downstream partners integrate activities into a unified effort for fully realised operational efficiency.
How is technology allowing for efficient supply chain planning?
Sophisticated and intelligent software tools are applicable throughout the SCP process. A look at current software capabilities illustrates how food businesses that implement this technology can optimise supply chain planning and achieve better results.
Forecasting
Specialised artificial intelligence (AI) tools can use predictive analytics to generate highly probable, data-driven market forecasts. AI allows users to model additional scenarios, determine their relative likelihood and analyse potential outcomes. For instance, a widespread drought may cause crop failure and elevated prices. AI can model how this will affect profitability, price and market demand while helping businesses identify alternative scenarios and reduce any potential impact on consumers and supply chain partners.
Production planning
In SCP, AI can determine how production can be scheduled to meet demand and determine resourcing requirements. It can even factor in expected downtime for routine equipment maintenance, and indicate where and when it should occur. Once again, alternative approaches and variations can be modelled:
- Farmers can decide whether to devote more or less land to certain crops
- Intermediaries can analyse logistics
- Manufacturers can determine whether they need to adjust production lines or methods
- Packaging firms can adjust production lines based on expected demand
Inventory planning
Intelligent software can use demand forecasts and production planning to determine optimum inventory levels and reorder levels for production inputs. This enables businesses throughout the supply chain to collaborate and negotiate with suppliers, or even automate ordering processes to reduce the likelihood of oversights and errors. Additionally, lead times can be analysed to determine reorder levels and minimise the risk of ingredient spoilage.
Risk management
AI tools allow businesses to generate strategies that can minimise the impact of upstream and downstream supply chain risks. With real-time monitoring during SCP execution, they can respond quickly when exposed to potential risks. For instance, Columbia remains one of the world’s largest coffee-producing countries but is subject to risks from political instability and climate change. If there are indications that yields may be severely reduced or supply chains disrupted, businesses can create contingency plans to avert shortages.
What are the benefits of supply chain planning?
Good SCP requires collaboration. For example, product manufacturers can collaborate directly with wholesalers and major retailers to measure consumer demand. This allows them to formulate production plans and collaborate with suppliers so that they know the specifications, volumes, and timing they will be expected to achieve. They will use this information to prepare their own raw material suppliers for expected demand.
By working together to meet consumer demand, supply chain partners can function more efficiently, making the most of market opportunities while also mitigating risks. This heightens customer satisfaction across the supply chain and fosters stronger business relationships.
With a responsive supply chain network that is prepared to meet demand, the risk of running out of stock or holding excess inventory of perishable ingredients like meat and dairy products is reduced. This saves money by reducing the amount of stock sold at discount prices ahead of expiration dates and minimising waste through inventory spoilage.
Effective inventory planning also benefits cash flow because there is greater certainty and a reduced need for extra inventory. Meanwhile, working capital can be used more profitably, for example, by leaving it in an interest-bearing account. With operations streamlined to meet demand and the supply chain sustaining their collaborative efforts, profitability can be enhanced across the board.
Overcoming the challenges of supply chain planning
Data quality and integration
Supply chain management and planning tools need accurate, timely, and correctly formatted data. Fortunately, solutions that can automatically capture and integrate data are already available. Besides ensuring that up-to-date information is always available, they limit opportunities for human error so that data is more accurate and reliable.
Change management
Managing change is always complex. Apart from resistance to change in your own business, you may experience pushback from supply chain partners. The use of SCP tools is already widespread, so implementation may not be as challenging as it formerly was. With the right partnerships to drive change and a mutual understanding of the benefits in store, negotiating compliance may be far easier than you may have expected.
Choosing the right AI solution
The tech sector does not always understand industry needs to the full. The food and beverage sector is characterised by complexity and a heightened need for regulatory compliance. Choose software that has been developed with the aid of food industry professionals. Similarly, scalability that makes your AI solution effective in both large and small business contexts will be key.
Supply chain planning best practices in the food industry
We have already captured several best practices in supply chain planning throughout this article. For example, we have examined the importance of evidence-based forecasting, the use of technology, and collaborating to realise efficiencies. However, there are additional points to consider as you move towards ever-more effective supply chain planning and execution.
Sustain collaboration throughout the plan execution
Supply chain partners should continue to collaborate throughout the execution phases of the supply chain plan. A shared platform for reports and updates ensures that everyone is on the same page. Although this principle applies to any business, it is of even greater importance in the food industry. At its most basic level, it impacts food security and prices for consumers while, at a higher level of needs-fulfilment, it affects customer satisfaction.
Update demand forecasts throughout the planned cycle
SCP should be an ongoing process. Markets are dynamic, and although you have embarked on a planned process, it may be necessary to adapt in the light of real-time information and unexpected events. A natural disaster may lead to consumers stockpiling non-perishable foods or an event that leads to economic uncertainty may lead to unforeseen bulk buying that reduces long-term consumer demand.
Set and manage key performance indicators
Supplier performance is a key factor in the execution of supply chain plans. Set agreed-upon KPIs to measure order fulfilment rates, delivery timelines, lead times, supply chain costs, and product quality. Provide regular feedback, and communicate when supplier performance fails to match specifications.
If this occurs frequently or quality issues seem likely to affect food safety, it may be time to seek alternative solutions. For instance, a supplier who fails to maintain the cold chain when transporting perishable food ingredients should detect the issue in real time, making alternative provisions for the timely delivery of fresh inventory. If they do not do so, production and sales could be negatively impacted.
Incentivise performance
There may be times when retailers’ demand forecasts are overly optimistic. This can be particularly damaging if they overestimate sales of perishable foods. If they fail to reorder per expectation the costs to manufacturers and their suppliers can be high, you must be sure to incentivise accuracy. If their sales forecasts are realistic, the supply chain benefits from cost savings. Retailers should be incentivised to make this possible, and this can easily be achieved by offering discounts when sales targets are reached.
Implement effective inventory management
The benefits of effective SCP can only be realised to the full when internal inventory management aligns with best practices. For example, a first-in-first-out (FIFO) approach to inventory management helps to limit spoilage. Track inventory management performance indicators to ensure that your business is making the most of any opportunities that flow from supply chain planning.
Retain a focus on traceability and sustainability
While cost savings are a primary goal for all businesses, sustainable sourcing is still vital. Traceability is important to food safety, regulatory compliance, reputation management, and overall sustainability. Your supply chain management software should provide the information you need to make best-practice sourcing decisions. According to Deloitte, a field-to-fork approach to traceability enhances consumer trust and leads to repeat purchases.
Supply chain planning and management software for the food industry
Foods Connected offers end-to-end supply chain management software so you can ensure compliance and realise cost savings at every point of the supply chain. This includes the capacity to audit supply chains to reduce risk and enhance product quality, optimise procurement by constantly monitoring market dynamics, and share real-time analytics across your entire supply chain network.
To find out more request a demo today.
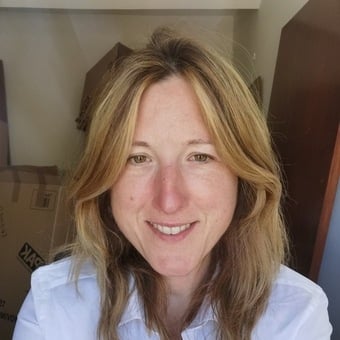
Greer McNally
Greer has over 15 years’ experience writing about trends in the food and retail sectors. She lives in a little village by the sea in Northern Ireland and loves creating content that informs how people think about the food industry. A recent career highlight was interviewing the legend that is Dr Temple Grandin.
Stay up to date
Stay up to date
Browse Posts
- August 2025
- July 2025
- June 2025
- May 2025
- April 2025
- March 2025
- February 2025
- January 2025
- December 2024
- November 2024
- October 2024
- September 2024
- August 2024
- July 2024
- June 2024
- May 2024
- April 2024
- March 2024
- February 2024
- January 2024
- December 2023
- November 2023
- October 2023
- September 2023
- August 2023
- July 2023
- June 2023
- May 2023
- April 2023
- March 2023
- December 2022
- November 2022
- October 2022
- September 2022
- August 2022
- July 2022
- June 2022
- May 2022
- April 2022
- March 2022
- February 2022
- January 2022
- December 2021
- November 2021
- October 2021
- August 2021
- July 2021
- June 2021