We sat down with three industry experts – Dr Stephanie Brooks, Dr Lorelei Gherman and Professor Jillian MacBryde – to discuss the benefits and the blockers of digital transformation for food businesses right now.
The agri-food industry is the largest manufacturing sector in the UK. A large and complicated machine, with a complex supply chain, it also comes with a significantly high sales value.
With so many actors at play then, perhaps it should come as no surprise that the sector has been slower than some other industries to embrace digitalisation.
But as AI grows in popularity and large high-street retailers encourage their suppliers to go digital, there appears to be an air of positivity around digital transformation. With this in mind, we sat down with three experts – Dr Stephanie Brooks, Dr Lorelei Gherman and Professor Jillian MacBryde – to get their thoughts on the topic.
Our experts on why it's a good time to digitise...
“We're in this new era of Industry 4.0 in the food industry,” says Dr Brooks. “It’s all about smart, autonomous processes within manufacturing - and to really avail of those opportunities such as artificial intelligence, we really need to be digital.”
“In turns that means that if you’re not digitised – or starting to be – then you’re in danger of missing out on some of these new industry developments.”
"If you’re not digitised – or starting to be – then you’re in danger of missing out on... new industry developments.”
Our experts on creating solutions for the modern food system...
Dr Gherman sees a range of industry challenges driving this solution-based thinking. There are general production issues, which digitalisation can easily address through robotics and automation; food and drink and agricultural obstacles, which can be addressed with innovation; and new developmental technologies, which can help, not just data-driven technologies, but also manipulation production.
“But everyone's value proposition and the value they can generate from any technology is going to be different,” admits Dr Brooks. “So, it's really important that technology providers are able to deliver tech that's adaptable and solutions that can be configured.”
“The immediate benefit comes from being able to understand data-driven management or data driven insights into your business."
“Of course, the immediate benefit comes from being able to understand data-driven management or data driven insights into your business,” she adds. “Having that data-driven insight helps businesses pave the way to optimise value in their supply chains in the future.”
Our experts on the barriers to digitisation...
As a manufacturing engineer, Dr Gherman deals with digitalisation on a daily basis. Some of the barriers she sees associated with innovation adoption are the same ones she encounters with adopting digitalisation.
“There's definitely a lot of traditional businesses that would work in food and drink manufacturing with traditional equipment - some are still using paper-based methods to collect data and keep quality checks. For these businesses, there’s definitely a knowledge and communication upscale needed for the staff to adopt digitalisation.”
“But this isn’t an unsurmountable obstacle. “There are ways to address this and ways for businesses to get support in upskilling their staff through training programmes.”
Our experts on early adoption...
All three experts agree that businesses often need to see digitalisation working for others before they commit themselves.
“No one wants to be an early adopter,” says Dr Gherman, “because that means taking a risk, and especially when you’re a food and drink manufacturing SME, your budget may be limited.”
She finds that sharing case studies is often helpful, but the biggest shift comes from industry encouragement. “Once a business starts receiving support from innovation agencies, research centres and innovation hubs such as InterAct, there is support for your road map to adopt digitalisation and innovation in-house.”
It is important for businesses to know that there is support available and it is free.
Professor MacBryde adds, “We've just done a survey with nearly 300 responses from manufacturers about their digital journey - and some of the things you've said exactly is what they're telling us. It's all about that reticence and a sense of uncertainty about the technology.”
There are other factors at play too. “There’s the element of cost and the other thing that kept up was about not having the capacity to free people up to do the training.”
Dr Gherman agrees. “Sometimes it’s not skills, it's the capacity to build in the training to upscale people."
Our experts on the benefits of investment...
“I think when we talk about digital transformation, we want to be able to demonstrate tangible benefits,” says Dr Brooks. “So, for example, that there was a cost saving that was associated with it.”
So when businesses consider investing in the technology, they can see tangible cost saving that benefits them or helps them direct the activities of their employees towards more value-adding activities rather than administrative resource-heavy activities.
“Opting in isn’t just about because your neighbour has adopted certain technologies,” agrees Professor MacBryde. “That doesn't necessarily mean it's for you. It's about looking at your business, looking at the people and your skill set and the industry.”
"Opting in isn’t just about because your neighbour has adopted certain technologies. It has to be right for you."
Automation is another part of the digital transformation package that brings its own benefits. Dr Brooks explains, “It gives you a lot of visualisation that would normally not be visible on the basis that information may be resided on an Excel spreadsheet or on paper.”
Dr Gherman has seen some of the businesses she works with benefit from a massive upturn in productivity – and quality – thanks to digitisation. “One manufacturer switched from a paper-based quality check manual process to a bespoke ERP solution. So they went from paper to handheld tablets and real-time visualisation of the factory data, and that enabled them to rapidly identify, communicate and react to quality issues.
"Their productivity used to be around 1000 tons of potatoes per week and just within the first six months of operations, the solutions enabled them to reduce the returns from customers by thousands of kilos. So a huge, huge, upturning productivity and quality.”
Our experts on how blockchain-like tech is being adapted to fit...
This a specialist digitalisation area for Dr Brooks concentrating on traceability. She explains, “ You can take all the great parts about blockchain - it's cryptographic ledger, signatures and security – and reinvent the technology in what we would call a centralised way. This allows you to keep the costs to a much more attainable region for the food industry."
This is an excerpt from our webinar on Overcoming barriers to digitalisation: adding value in the agri-food sector. To listen to the entire discussion click on the link below.
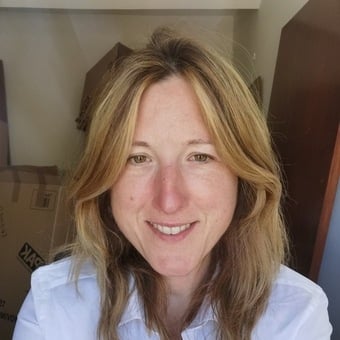
Greer McNally
Greer has over 15 years’ experience writing about trends in the food and retail sectors. She lives in a little village by the sea in Northern Ireland and loves creating content that informs how people think about the food industry. A recent career highlight was interviewing the legend that is Dr Temple Grandin.
Stay up to date
Stay up to date
Browse Posts
- August 2025
- July 2025
- June 2025
- May 2025
- April 2025
- March 2025
- February 2025
- January 2025
- December 2024
- November 2024
- October 2024
- September 2024
- August 2024
- July 2024
- June 2024
- May 2024
- April 2024
- March 2024
- February 2024
- January 2024
- December 2023
- November 2023
- October 2023
- September 2023
- August 2023
- July 2023
- June 2023
- May 2023
- April 2023
- March 2023
- December 2022
- November 2022
- October 2022
- September 2022
- August 2022
- July 2022
- June 2022
- May 2022
- April 2022
- March 2022
- February 2022
- January 2022
- December 2021
- November 2021
- October 2021
- August 2021
- July 2021
- June 2021